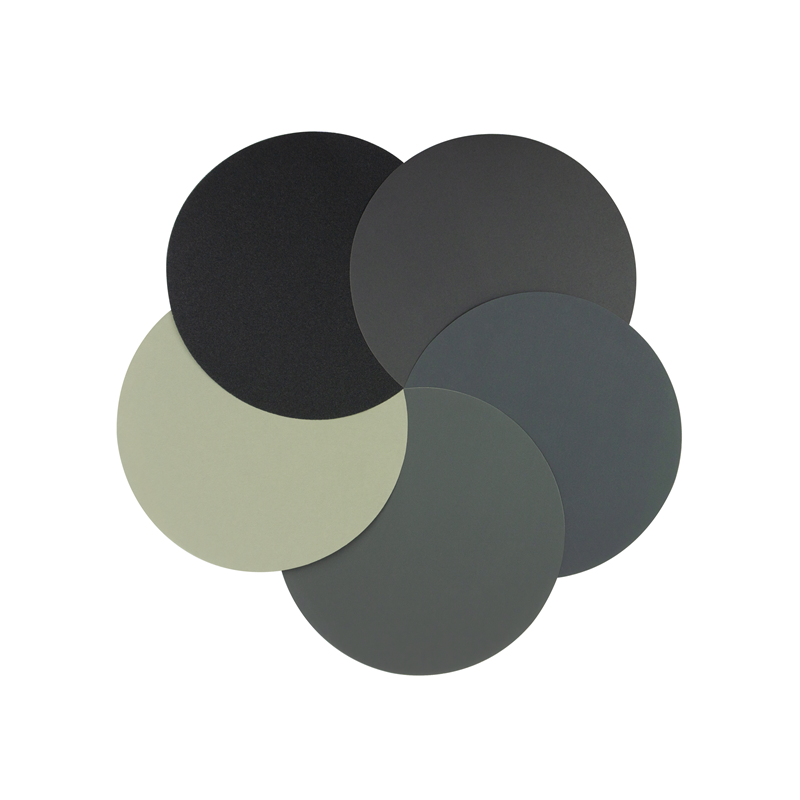
There are various methods of sampling. It can be flexibly selected according to the size of the sampled parts, material properties, and current actual conditions. The most commonly used method is metallographic cutting machine grinding wheel (metallographic cutting sheet) cutting. Generally, materials with lower hardness (less than 230HBW) such as low carbon steel, medium carbon steel, gray cast iron, non-ferrous metals, etc. can be machined with saws, cars, planers, etc. For materials with higher hardness (about greater than 450HBW) such as white cast iron, cemented carbide, and brittle materials such as quenched parts, the hammering method can be used to select the size and size from the broken fragments. For large section parts or high manganese steel parts, etc., oxyacetylene flame gas cutting can be used, but a margin larger than 20mm must be reserved so that the heat affected zone of gas cutting can be removed during sample grinding.
Regardless of the sampling method, it is necessary to prevent tissue changes caused by temperature rise, or plastic deformation caused by force.