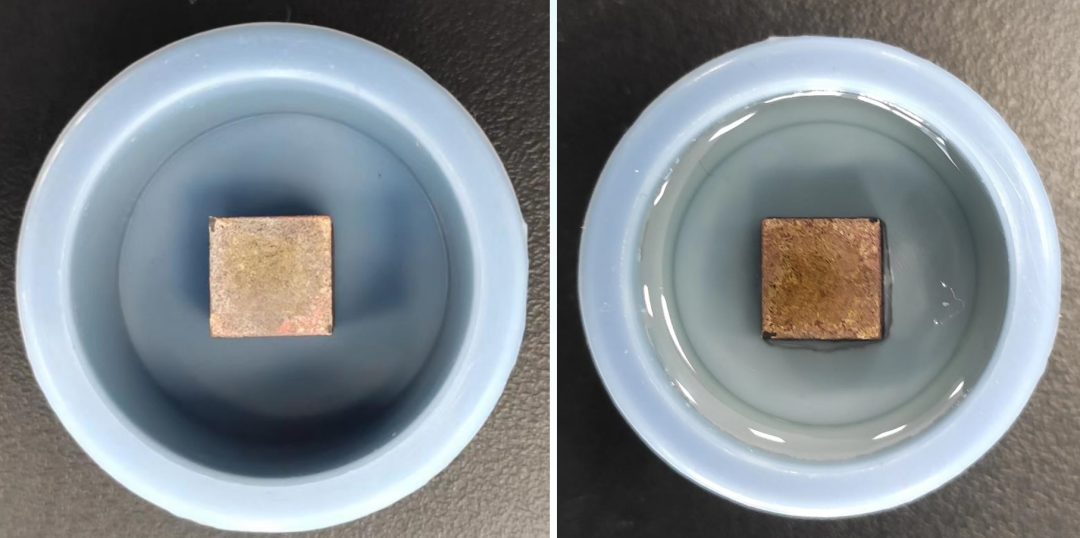
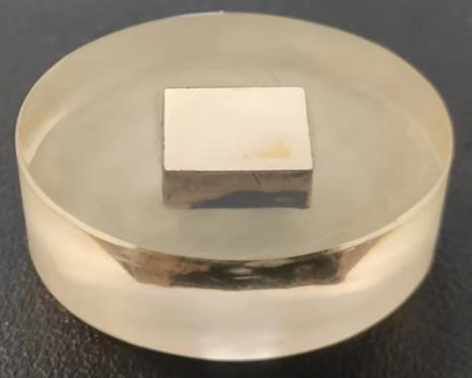
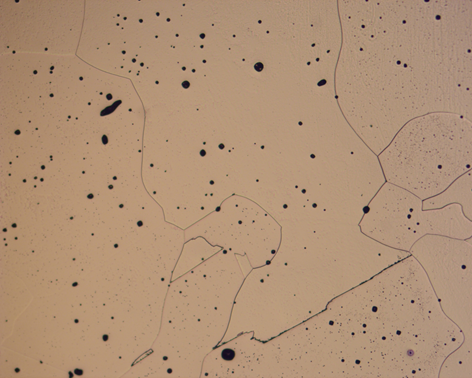
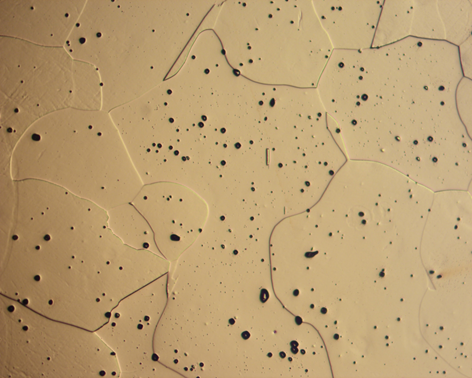
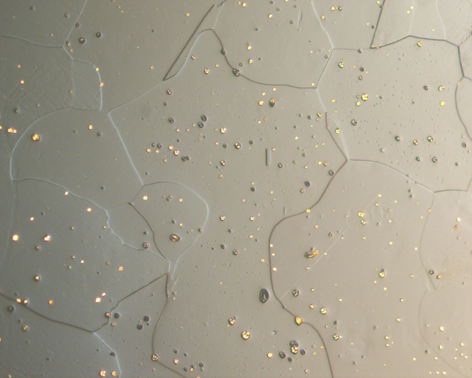
Cu-12sn alloy is annealed sample, its hardness is low, and it is easy to produce deep deformation layer during grinding and polishing. Therefore, when grinding, we should try to start from fine sandpaper, and the strength of manual grinding must be light. Each sandpaper should ensure that the deformation layer produced by the sandpaper is removed.
When polishing, the deformation layer produced by grinding should be removed in the coarse polishing stage. For this reason, coarser polishing particles and longer time can be used on the hardness machine weaving cloth. Use with lubricant.
In fine polishing, soft short velvet polishing cloth should be used for chemical polishing in order to remove the deformation layer and scratch caused by rough polishing.
It is not practical to get a perfect sample in one lapping and polishing corrosion. If conditions are limited, repeated polishing and etching operations are required. That is, after the corrosion has a scratch, the final piece of mechanical chemical polishing is done again and then the corrosion is repeated, and this step is repeated until there is no scratch.
Fine casting speed can be adjusted in the range of 150~300rpm, fast at the beginning, and low speed at the end. Keep the pressure on your hands light and rotate against the chassis.
Corrosion with a mild caustic, using the drip etching method.
The black spots in the metallography are silica and silicate inclusions.