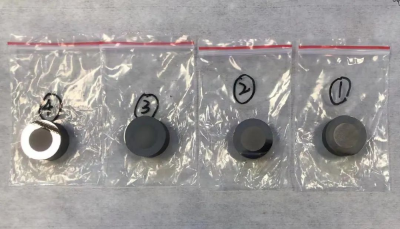
01 Grinding
Grind the specimen with Alpha-600 automatic grinder&polisher,diamond grinding disc P400→P1500→P3000;
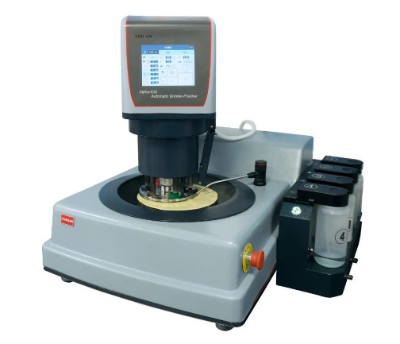
Alpha-600 automatic grinder&polisher
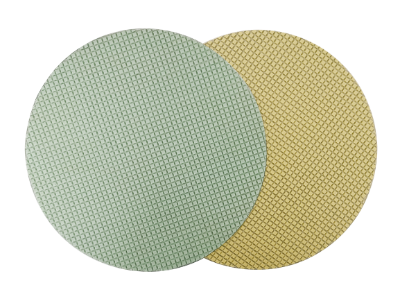
Diamond grinding disc
Equipment |
Alpha-600 automatic grinder&polisher |
Consumables |
Diamond grinding disc:P400,P1500,P3000 |
Parameter |
Pressure:15N,Speed:130rpm,TIime:2Min |
02 Rough Polishing
Polish the specimen with Alpha-600 automatic grinder&polisher,use NL polishing cloth first, then use 3μm polycrystalline diamond suspension with colloidal silica suspension.
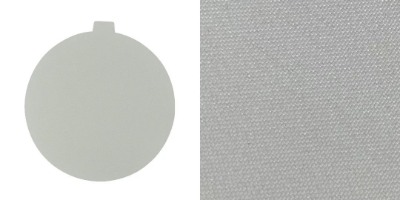
NL-CP white fiber polishing cloth
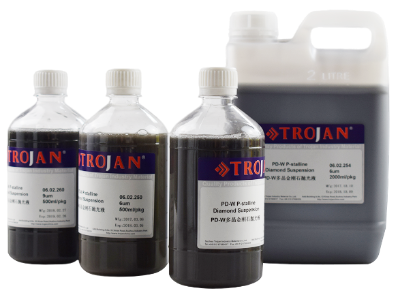
PD-W polycrystalline diamond suspension
Equipment |
Alpha-600 automatic grinder&polisher |
Consumables |
NL polishing cloth,3μm polycrystalline diamond suspension, colloidal silica suspension |
Parameter |
Same direction:150rpm,Pressure:20N,Time: 300s |
03 Fine polishing
Polish the specimen with Alpha-600 automatic grinder&polisher,use ET polishing cloth with 50nm colloidal silica suspension to do fine polishing.
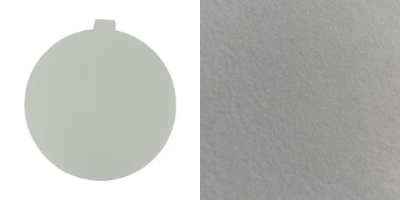
ET-JP white synthetic velvet polishing cloth
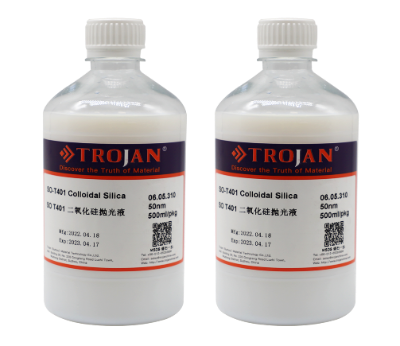
SO T401 Colloidal silica suspension
Equipment |
Alpha-600 automatic grinder&polisher |
Consumables |
ET polishing cloth,50nm colloidal silica suspension |
Parameter |
Same direction:120rpm,Pressure:10N,Time: 60s |
04 Observation
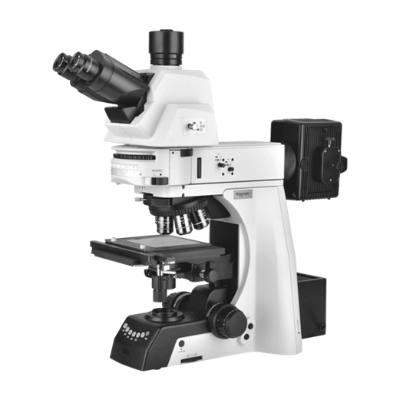
Equipment |
MN 60 series microscope |
Parameter |
50×→500× |
05 Analysis
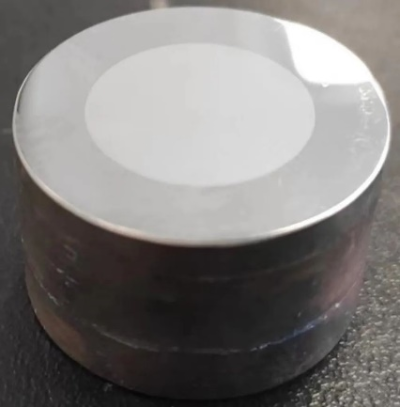
2
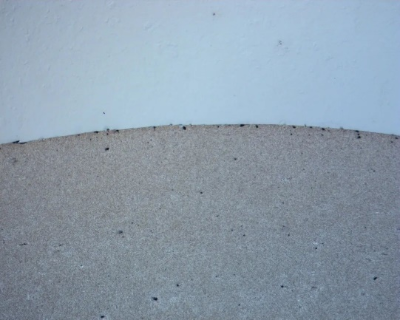
50X
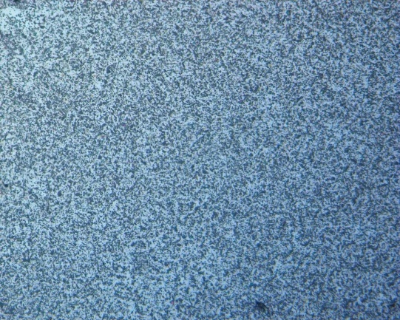
500X
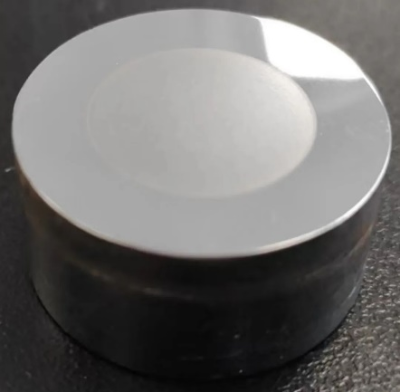
3
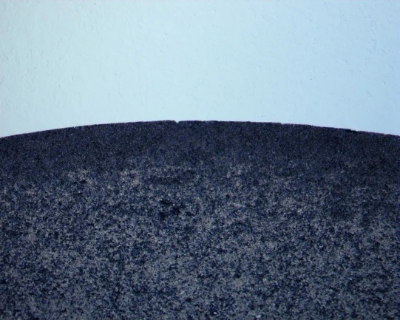
50X
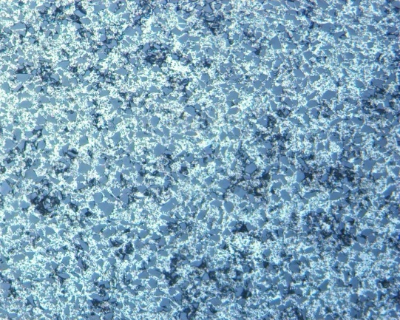
500X
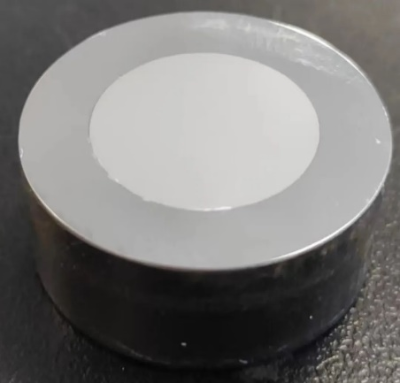
L2
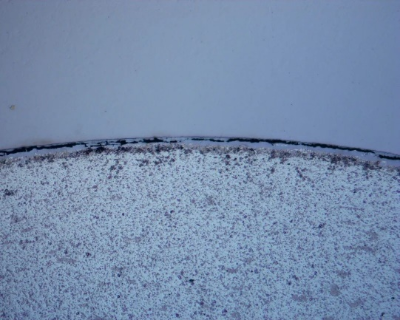
50X
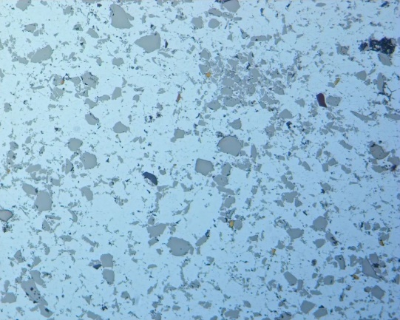
500X
The hardness of Boroncarbide is very high, and it is difficult to grind with general silicon carbide abrasive paper, so diamond grinding discs are used for grinding.
Due to the disparity in hardness between the substrate and the conforming boron carbide phase, in order to prevent embossing, first use a hard lint-free woven cloth for rough polishing. For boron carbide, silicon dioxide should be used for mechanical chemical polishing to obtain a better polished surface.
It can be seen from the picture that the distribution of boron carbide in the L2 sample is uneven, and the fine particles are seriously aggregated in some areas.