Both zirconium alloys and pure zirconium are metals with a close-packed hexagonal crystal structure, which are characterized by being relatively soft and prone to ductility. Therefore, the zirconium alloy is easy to leave a deep deformation layer and scratches that are difficult to remove during the grinding and polishing process. In addition, twinning may occur if the force is not properly controlled during cutting, mounting and grinding. Therefore, the metallographic preparation of zirconium and its alloys should be very careful.
01 Equipment and consumables
Equipment |
Trojan Alpha-600 automatic grinder&polisher; Leica DM2700M metallographic microscope; Hairdryer; |
Consumables |
Ethanol;Degreasing cotton; Trojan PL-W Polishing lubricant; Trojan SiC metallographic abrasive paper(P2000;P2500); Trojan YS-JP white fiber polishing cloth(8in); Trojan ET-JP white synthetic velvet polishing cloth(8in); Trojan 3μm polycrystalline diamond suspension; Trojan 1μm polycrystalline diamond suspension ; Trojan 0.05μm non-crystallizing silica suspension; |
02 Sample preparation process
2.1-Grinding
Due to the good surface condition of the sample,so polish the specimen with Alpha-600 automatic grinder&polisher, abrasive paper P2000→P2500(The surface of the sample is in good condition, if it is not treated, it can start from P400).
Equipment |
Alpha-600 automatic grinder&polisher |
Consumables |
Abrasive paper:P2000;P2500 |
Parameter |
Pressure:15N,same direction:200rpm,time:120s |
2.2-Plane polishing
Polish the specimen with Alpha-600 automatic grinder&polisher, use YS polishing cloth with 3μm polycrystalline diamond suspension first,then use it with 1μm polycrystalline diamond suspension for plane polishing. Diamond polishing liquid should be used in conjunction with polishing lubricant.
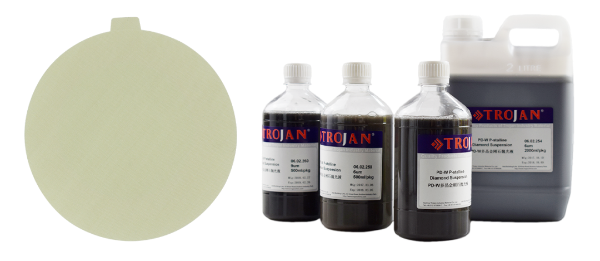
Equipment |
Alpha-600 automatic grinder&polisher |
Consumables |
YS polishing cloth,3μm/1μm polycrystalline diamond suspension,PL-W polishing Lubricant |
Parameter |
Pressure:22N,same direction:150rpm,time:300s |
2.3-Fine polishing
Polish the specimen with Alpha-600 automatic grinder&polisher,use ET polishing cloth with 0.05μm non-crystallizing silica suspension.(Add 25% ammonia water and 3% hydrogen peroxide to the silica polishing solution)
Equipment |
Alpha-600 automatic grinder&polisher |
Consumables |
ET polishing cloth,0.05μm non-crystallizing silica |
Parameter |
Pressure:20N,reverse direction:120rpm,time:600s |
2.4-Observation
Equipment |
Leica DM2700M metallographic microscope |
Consumables |
|
Parameter |
50×→500× |
03 Analysis
Zirconium has a low hardness and is prone to embedment and scratch defects. The use of chemical mechanical polishing in fine polishing can effectively remove the deformation layer on the surface of the sample to obtain a bright and perfect surface.
It should be pointed out that the quality of the customer's hot mounting is poor, and there is a gap between the resin and the sample. In order to prevent cross-contamination between different abrasive particles, it is recommended to perform ultrasonic cleaning between each track. The hot mounting material is not completely burned through and fused, and after grinding and polishing, there are lumps and discoloration, and it is recommended to improve.